90% WNiMoFe Tungsten Alloy for Die Casting
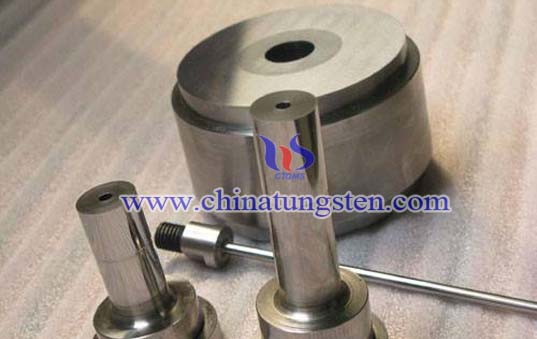
Thermal fatigue is one of reasons of tool end of life. Higher tensile strength and better thermal conductivity has the function of minimizing thermal fatigue and thereby improve tool life. Tool steel does a good job in many die casting applications, but its life decreases as casting temperatures increase. Heat checking is a thermo-mechanical fatigue process caused by thermal cycling, which creates cyclic stresses and strains in the cavity surface. Typical damage is the gradual growth of a network of cracks. 90% WNiMoFe tungsten alloy has low thermal expansion and high thermal conductivity which are fundamental for heat checking resistance. The low thermal expansion allows for low thermal stress. A high thermal conductivity reduces the thermal gradients and thereby the thermal stress by cooling the casting faster.
What is more, low erosion. Erosion of the die is a problem. 90% WNiMoFe tungsten alloy provides a low erosion rate due to its chemical resistance. This occurs because molten aluminum dissolves tool steel. Aluminum does not dissolve 90% WNiMoFe tungsten alloy, therefore you have a longer die life. This means you don't have to change the die or core rods as often which results in less downtime. Die life can be up to 10 times longer with 90% WNiMoFe tungsten alloy.
We can supply 90% WNiMoFe tungsten alloy in shape of rod, plate, block and finished parts according to the user's drawing.